The procedure of CNC machining requires the use of a computer to regulate machine tools for an extra trustworthy and consistent outcome. This innovation converts CAD (computer-aided design) designs straight right into machine-readable code, which guides the machining procedure. The outcome is that manufacturers can create components with regular quality and precision, minimizing waste and the threat of error in production. When it comes to copper, which can be fairly challenging to device because of its thermal conductivity, high ductility, and propensity to work-harden, CNC modern technology provides the flexibility required to resolve these problems efficiently. Specialized tools and methods are often employed to optimize the machining process, which can include utilizing reducing devices covered with tough products to minimize wear and improve performance when dealing with soft metals like copper.
Discover copper cnc machining exactly how copper CNC machining combines sophisticated modern technology with lasting practices to produce intricate, high-precision elements, driving advancement throughout sectors such as electronic devices, automotive, and aerospace.
Among the key benefits of CNC machining copper is the ability to produce complicated shapes that traditional machining methods might not suit. The high accuracy possible with CNC innovation enables makers to produce firmly toleranced functions that are vital in lots of applications. In the electronic devices market, for example, the demand for parts with marginal resistances is extremely important, as digital gadgets diminish and more intricate. CNC machining facilitates the manufacturing of micro-components with such great resistances, allowing developments in smart tools, wearable modern technology, and various other consumer electronics. In addition, the repeatability of the CNC machining procedure makes sure that mass production of copper parts maintains harmony, hence satisfying strict industry standards.
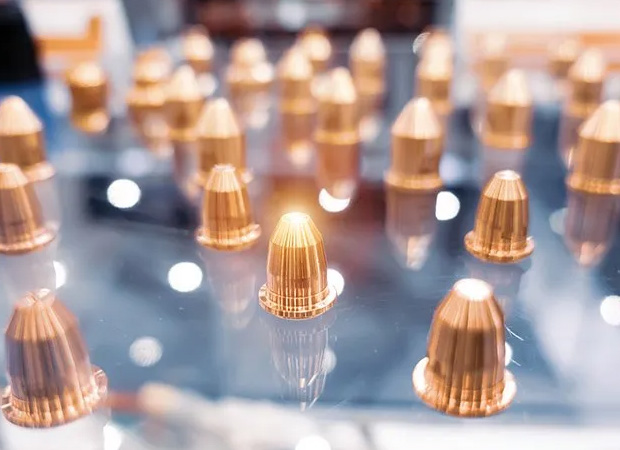
Temperature monitoring plays a vital function in the CNC machining of copper due to its capacity to carry out heat rapidly. High-speed machining can bring about substantial warm generation, which may detrimentally affect the properties of the copper and worsen tool wear. Subsequently, CNC machinists commonly turn to advanced air conditioning methods, such as flooding coolant systems and haze lubrication, to manage warmth and prolong tool life. By regulating the temperature throughout machining, producers can attain much better surface coatings, enhance precision, and produce components with enhanced mechanical properties. In addition, with the introduction of modern technologies like high-pressure cooling systems and innovative reducing fluid solutions, CNC machining can accomplish optimal efficiency while properly taking care of thermal impacts.
The sustainability aspect of CNC machining copper is not to be neglected. CNC machining, combined with lasting practices, can reduce waste by permitting producers to make use of scrap copper from various other processes.
Along with sustainability, cost-effectiveness is one more essential element for makers picking CNC machining for copper components. Though the preliminary financial investment in CNC machinery may be considerable, the long-lasting advantages can outweigh the expenses. CNC machining offers a decrease in labor expenses as a result of its automatic nature and lessens the need for considerable manual intervention. The precise control & repeatability offered by CNC innovation decreases scrap prices, decreasing material costs. Furthermore, for tiny to tool batch production runs, CNC machining can confirm more cost-effective contrasted to traditional machining processes, as it enables for smooth adjustments and layout adjustments without extensive retooling. This ability to pivot swiftly can be helpful, specifically in fast-paced industries where market demands can shift suddenly.
As modern technology evolves, the functionalities within CNC systems are expanding, further boosting the capacities of copper machining. The combination of simulation software application enables producers to forecast possible concerns prior to the machining process begins. These simulations enable far better preparation of tool paths and elucidate how the copper product will certainly respond throughout the machining process. By recognizing and resolving prospective difficulties in advance, firms can decrease downtime and boost productivity, developing a smoother functional circulation.
Experienced machinists have to be proficient in analyzing style requirements, selecting the ideal tools, and readjusting machining parameters to alleviate concerns connected with copper's unique machining attributes. Hybrid machining, which integrates traditional CNC machining techniques with additive production, is emerging as a sensible technique for generating intricate copper parts, blending the staminas of both modern technologies and potentially reinventing how makers approach copper production.
In the world of r & d, CNC machining is aiding the exploration of brand-new copper alloys to enhance efficiency further. By synthesizing copper with materials such as tin, aluminum, or nickel, suppliers can engineer compounds that have actually improved stamina, electrical performance, and resistance to put on and corrosion. These advancements can lead to emerging applications in markets that count heavily on conductive materials, such as sustainable power and electrical vehicles. As international industries work towards better power efficiency, copper's function as a conductor in digital circuits will certainly stay paramount, driving demand for sophisticated machining remedies.
The aerospace and automobile markets are additionally keen adopters of copper CNC machining, particularly where lightweight elements are of critical importance. The combination of copper's lightweight nature and exceptional electrical and thermal conductivity makes it a perfect option for elements such as electric calls, warmth exchangers, and wiring systems. As the change toward hybrid and electric automobiles proceeds, the need for high-performance copper components will likely surge, thereby pushing the requirement for innovative CNC machining techniques that make certain performance and quality in production. From a manufacturing standpoint, the ability to innovate rapidly and deliver precision-engineered parts becomes progressively vital in dealing with the arising needs of these fast-evolving fields.
As CNC machining modern technology proceeds to create, it enables more automation, where basic procedures such as tool adjustments, inspections, and upkeep can be set right into the manufacturing cycle. This development indicates that makers will be able to attain greater efficiency levels, shorter lead times, and better adaptability in suiting personalized demands or variants in style. Because of this, services that take part in CNC machining operations are better matched to pivot in feedback to the changes in customer and market needs, promoting growth in a progressively affordable landscape.
Discover countersink size chart exactly how copper CNC machining merges innovative modern technology with sustainable practices to produce detailed, high-precision elements, driving development across sectors such as electronics, automobile, and aerospace.
The global industry for CNC machining of copper is experiencing considerable growth, affected by aspects such as the rise of clever innovations, electric vehicles, and recurring efforts to enhance power performance across various applications. It mirrors an assembling trend where organizations accept digital production methods, assisting form the future of production. Establishing partnerships with suppliers, modern technology companies, and academia can boost accessibility to the current technologies and understanding within the field, cultivating a collective environment that drives forward-thinking campaigns. In this development, skill and training growth stay paramount; spending in workforce education and learning on CNC machining methods, innovations, and product sciences will certainly empower suppliers to stay in advance of the curve.
As industries develop and the limits of modern technology increase, embracing CNC machining's potential will be crucial to understanding unprecedented growth and innovation in the usage of copper items. The harmony of copper's product properties with advanced CNC machining techniques declares a brand-new age in which sustainability, efficiency, and precision job together to create revolutionary components that will define the future of production and beyond.